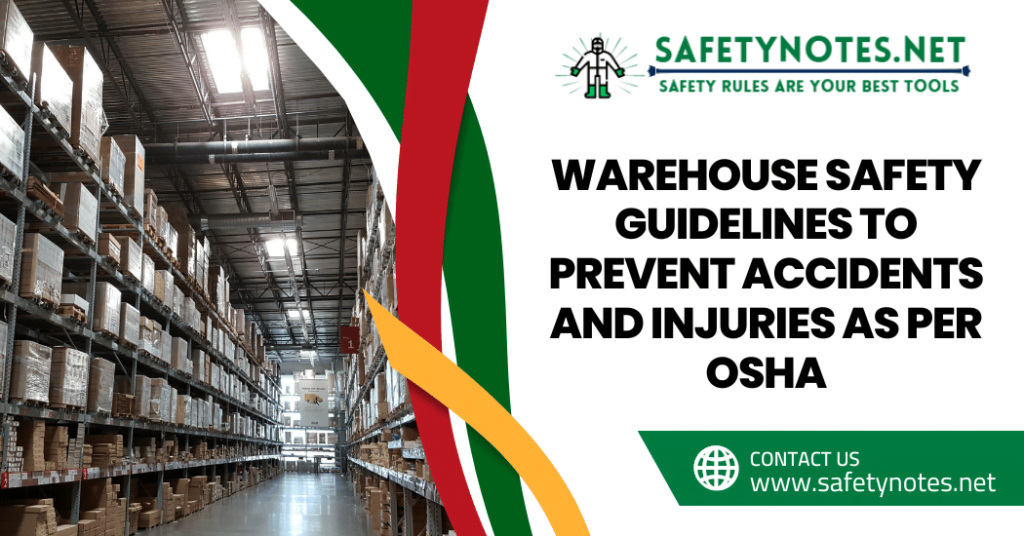
Warehouse workers play a vital role in the supply chain, ensuring that goods are stored, organized, and shipped efficiently. However, working in a warehouse environment comes with inherent risks and hazards that can lead to injuries and accidents if not properly addressed. In this comprehensive guide, we will explore the various hazards faced by warehouse workers and the necessary Warehouse Safety precautions to ensure their safety. We will also discuss the responsibilities of both employers and employees in maintaining a safe working environment. Let’s dive in!
1. Warehouse Hazards and Their Impacts
Physical Hazards
Physical hazards in a warehouse can result from the operation of heavy machinery, the use of forklifts, and unsafe storage practices. These hazards include:
- Falling objects: Improperly stacked materials or poorly secured loads can lead to falling objects, posing risks to workers below.
- Slip, trip, and fall hazards: Cluttered aisles, slippery floors, and uneven surfaces can cause workers to slip, trip, or fall, resulting in injuries.
- Forklift accidents: Forklifts are essential tools in a warehouse, but improper operation can lead to collisions, crushing incidents, or tip-overs.
- Pinch points and entanglements: Moving conveyor belts, machinery, or equipment can trap workers’ body parts, causing severe injuries.
Chemical Hazards
Chemical hazards in a warehouse arise from the storage and handling of hazardous materials. Some potential risks include:
- Exposure to harmful substances: Improper storage or handling of chemicals can lead to spills or leaks, exposing workers to harmful fumes or liquids.
- Fire and explosion risks: Combustible or flammable materials, if not stored correctly, can create fire hazards with potentially catastrophic consequences.
Ergonomic Hazards
Ergonomic hazards result from repetitive tasks, awkward postures, and manual lifting, leading to musculoskeletal disorders (MSDs). Common ergonomic hazards in a warehouse include:
- Improper lifting techniques: Frequent manual lifting of heavy loads can strain workers’ backs and result in back injuries.
- Awkward postures: Prolonged bending, reaching, or twisting can cause strain on the body and lead to discomfort and MSDs.
- Repetitive motions: Performing the same tasks repeatedly without sufficient breaks can cause strain on muscles and joints.
These hazards can have severe impacts on workers’ health and well-being, affecting their productivity and quality of work.
2. Precautions and Safety Measures
Forklift Safety
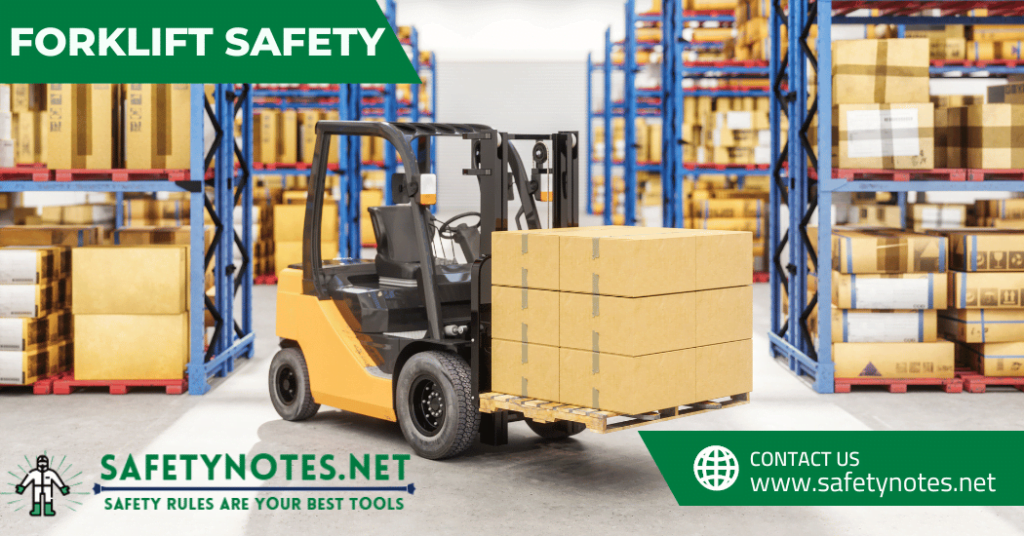
Forklifts are indispensable tools in warehouses, but their safe operation is critical to preventing accidents. Employers should:
- Ensure operators are trained and certified: Forklift operators must receive proper training and certification to operate the equipment safely.
- Conduct regular maintenance checks: Regular inspections and maintenance of forklifts help identify potential issues before accidents occur.
- Provide appropriate safety equipment: Forklift operators should wear personal protective equipment, such as gloves and eye protection.
- Prohibit smoking and open flames: Smoking and open flames should be strictly prohibited in areas where forklifts are operated or battery charging takes place.
- Ensure proper battery handling: Battery charging should only take place in designated areas, and employees exposed to battery acids should have access to eyewashing and safety showers.
Housekeeping and Cleanliness
A clean and organized warehouse is crucial for maintaining a safe working environment. To prevent accidents and injuries:
- Keep aisles and walkways clear of clutter and obstructions.
- Regularly inspect and maintain the warehouse for hazards.
- Address spills promptly and use warning signs if needed.
- Ensure proper lighting to enhance visibility.
Material Handling Safety
Safe materials handling practices are essential to prevent injuries from falling objects or improper storage. Employers should:
- Maintain safe clearances: Adequate aisle clearances and loading dock safety measures should be in place to prevent collisions and entrapments.
- Properly stack materials: Materials should be stacked evenly and straight, with heavier loads placed on lower or middle shelves to maintain stability.
- Use proper lifting techniques: Employees should be trained in proper lifting techniques to avoid back injuries and Musculoskeletal disorders (MSD).
- Keep work areas well-lit and clean: Proper lighting and well-maintained work surfaces help reduce the risk of accidents and improve overall safety.
Hazard Communication Safety
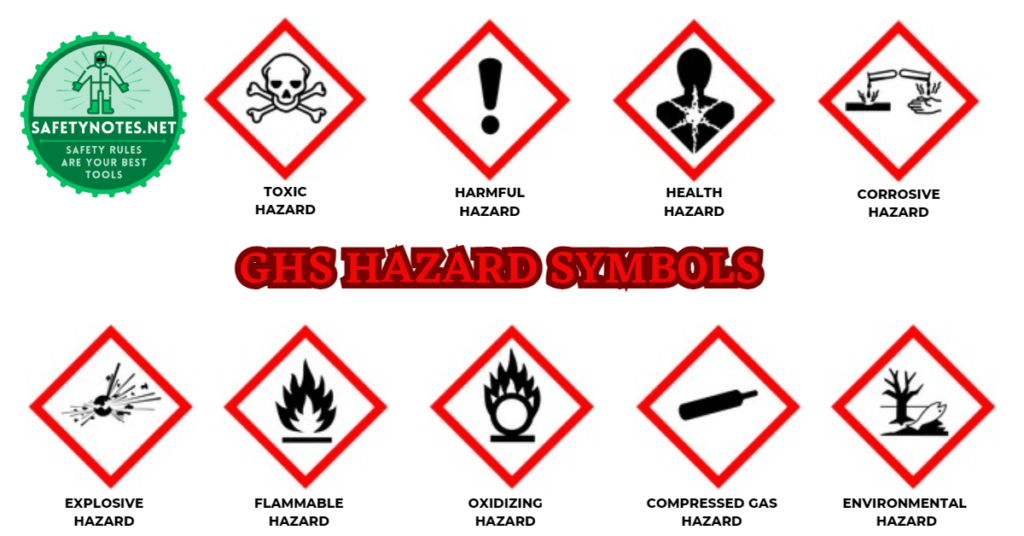
Proper communication and handling of hazardous materials are critical in a warehouse environment. Employers should:
- Maintain Material Safety Data Sheets (MSDS): Each chemical used in the facility should have an updated MSDS to inform workers of potential risks.
- Train employees on chemical hazards: Workers should be educated on the risks associated with the chemicals they handle and the appropriate safety measures.
- Provide spill cleanup kits: In areas where chemicals are stored, spill cleanup kits should be readily available to respond to potential accidents.
- Enforce the use of personal protective equipment: Proper PPE, such as gloves and goggles, should be provided and enforced to protect workers.
Personal Protective Equipment (PPE)
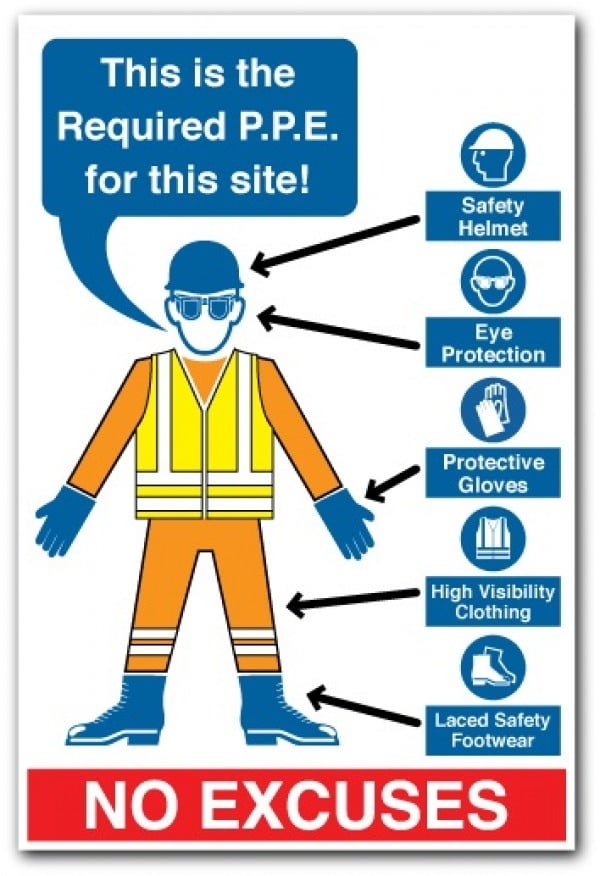
PPE plays a crucial role in safeguarding workers from various hazards. Employers should:
- Provide appropriate PPE: Employers should ensure that workers have access to the right PPE for the specific tasks they perform.
- Train employees on PPE use: Workers should receive proper training on the correct use and maintenance of their PPE.
- Store chemicals safely: Chemicals should be stored according to manufacturer recommendations and local or national fire codes.
By implementing these precautions, employers can significantly reduce the risk of accidents and injuries in the warehouse.
Emergency Action Plans and Evacuation
Emergency plans are vital for ensuring quick and efficient responses to potential hazards:
- Develop comprehensive evacuation procedures and emergency action plans.
- Conduct drills and training to familiarize employees with emergency protocols.
- Have designated emergency exits and ensure their accessibility.
3. Responsibilities of Employers and Employees
Both employers and employees share the responsibility of maintaining a safe and healthy warehouse environment. Each party has specific roles to play in ensuring workplace safety:
Employer Responsibilities
- Provide a safe working environment: Employers must identify potential hazards and take measures to eliminate or minimize them.
- Conduct regular safety training: Employers should ensure that all employees are adequately trained in the safe operation of equipment and handling of hazardous materials.
- Implement safety policies and procedures: Employers should establish clear safety guidelines and enforce their implementation.
- Provide necessary safety equipment: Employers must supply the appropriate PPE and safety tools to protect workers from potential hazards.
- Maintain compliance with OSHA standards: Employers should stay up-to-date with OSHA regulations and ensure their workplace meets all safety requirements.
- Encourage reporting and communication: Employers should encourage open communication between workers and management regarding safety concerns and incidents.
Employee Responsibilities
- Follow safety guidelines and procedures: Employees should adhere to all safety protocols and guidelines established by the employer.
- Use PPE as required: Workers must wear the necessary PPE when handling hazardous materials or operating equipment.
- Report safety hazards: Employees should promptly report any safety hazards or incidents to their supervisors or managers.
- Participate in safety training: Workers should actively engage in safety training programs and seek clarification if they have any questions.
- Promote a culture of safety: Employees should actively contribute to a safe workplace by maintaining clean and organized work areas and assisting in identifying potential hazards.
By working together, employers and employees can create a safe and productive warehouse environment for everyone.
4. Warehouse Safety Guidelines and Best Practices
General Safety Measures
- Keep aisles and walkways clear: Clutter-free aisles and walkways prevent trip and fall hazards.
- Conduct regular equipment inspections: Regular inspections of machinery and equipment help identify and address potential issues.
- Promote proper ergonomics: Ergonomic workstations and proper lifting techniques reduce the risk of Musculoskeletal disorders (MSD).
- Display safety signs and labels: Clear signs and labels provide visual cues and safety reminders to workers.
- Provide first aid and emergency response: Having first aid supplies readily available and emergency response plans in place can save lives.
Proper Materials Storage
- Stack materials safely: Materials should be stacked securely to prevent falling hazards.
- Store hazardous materials separately: Chemicals should be stored away from flammable or combustible materials.
- Use appropriate storage equipment: Racks, shelves, and pallets should be sturdy and suitable for the materials they hold.
Manual Lifting/Handling Techniques
- Train workers in proper lifting techniques: Employees should be trained on how to lift and handle heavy objects safely.
- Use mechanical lifting aids: When possible, mechanical lifting equipment should be used to reduce the risk of injury.
- Avoid overexertion: Workers should know their physical limits and avoid pushing themselves beyond what they can safely handle.
Evacuation Plans and Procedures
- Develop and communicate emergency plans: Employees should know the evacuation procedures and assembly points in case of emergencies.
- Conduct periodic drills: Regular evacuation drills help ensure that all workers know how to respond during emergencies.
- Train employees in fire safety: Workers should be educated on fire prevention and how to use fire extinguishers.
5. Compliance with OSHA Standards
Voluntary Protection Programs
OSHA’s Voluntary Protection Programs (VPP) recognize employers and workers who have implemented effective safety and health management systems. Businesses that meet VPP criteria demonstrate exemplary safety practices and receive recognition for their commitment to workplace safety. Many warehousing companies actively participate in VPP and share their expertise to mentor other businesses.
Alliance Programs
Alliance programs allow organizations committed to workplace safety to collaborate with OSHA in preventing injuries and illnesses. Several alliances impact the warehousing industry, including partnerships with the Retail Industry Leaders Association, the Industrial Truck Association, and the International Warehouse Logistics Association. These alliances promote safety, provide resources, and support initiatives to improve warehouse safety.
6. Conclusion
Warehouse worker safety is a crucial aspect of maintaining a productive and efficient supply chain. Identifying and addressing hazards, implementing safety measures, and fostering a culture of safety are essential in ensuring the well-being of employees. Employers and workers must collaborate and take their responsibilities seriously to prevent accidents and injuries in the workplace. By complying with OSHA standards and best practices, warehouse operators can create a safe and supportive environment where employees can thrive.
7. FAQs (Frequently Asked Questions)
Q1: What are the common physical hazards in a warehouse?
A1: Common physical hazards in warehouses include falling objects, slip, trip, and fall hazards, forklift accidents, and pinch points and entanglements.
Q2: How can forklift accidents be prevented in warehouses?
A2: Forklift accidents can be prevented by ensuring proper forklift operator training, conducting regular maintenance checks, providing appropriate safety equipment, and enforcing safety regulations.
Q3: How can ergonomic hazards be minimized in a warehouse?
A3: To minimize ergonomic hazards, warehouse operators can implement proper lifting techniques, provide ergonomic workstations, and encourage breaks to prevent repetitive motions.
Q4: What is the employer’s responsibility regarding safety in a warehouse?
A4: Employers are responsible for providing a safe working environment, conducting safety training, implementing safety policies, and ensuring compliance with OSHA standards.
Q5: How can employees contribute to warehouse safety?
A5: Employees can contribute to warehouse safety by following safety guidelines, using personal protective equipment, reporting safety hazards, and actively participating in safety training programs.
By prioritizing safety and implementing effective measures, warehouses can protect their workers and achieve higher productivity in their operations. Warehouse worker safety is a shared responsibility that requires continuous effort and commitment from all stakeholders involved. Let us work together to create safer warehouse environments for everyone.
Q6: What is the role of OSHA in warehouse safety?
A6:OSHA oversees workplace safety by setting and enforcing standards, conducting inspections, and providing resources to promote safe working conditions.
Q7: How can employees prevent musculoskeletal disorders (MSD)?
A7:Employees can prevent MSDs by using proper lifting techniques, utilizing ergonomic equipment, and taking periodic rest breaks.
Q8: What resources are available for warehouse safety?
A8: OSHA offers e-tools, publications, and alliances with industry associations to assist employers in improving warehouse safety.