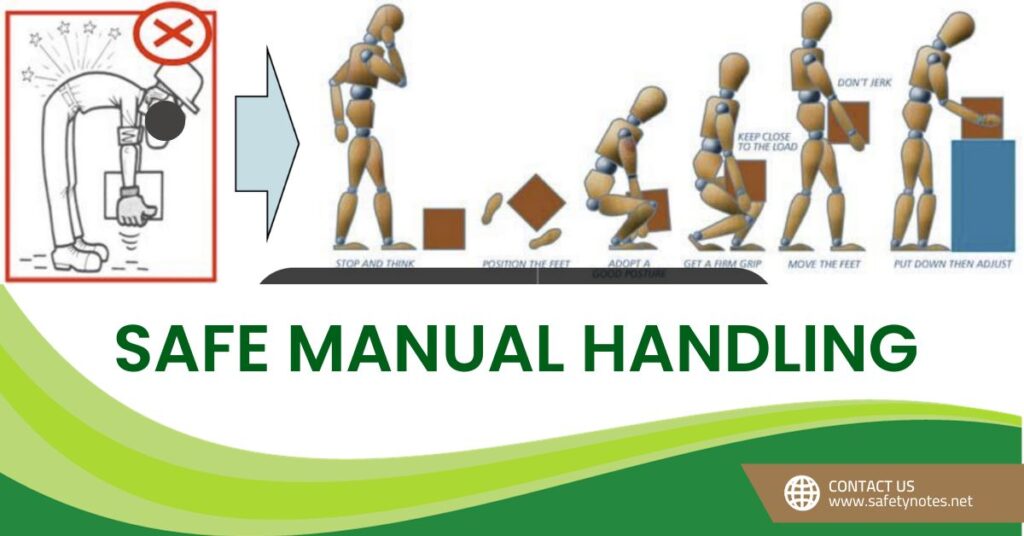
Manual handling is a common activity in many workplaces, but it can also pose significant risks to workers’ health and safety. According to the Health and Safety Executive (HSE), manual handling causes over a third of all workplace injuries, including musculoskeletal disorders (MSDs), such as back pain, sprains, strains, and hernias. Manual handling also accounts for a large proportion of work-related ill health, absenteeism, and reduced productivity2.
In this article, we will provide an in-depth guide on what manual handling is, why it is important, what are the hazards and risks associated with it, and how to prevent and reduce them. We will also cover the legal requirements and best practices for manual handling, as well as the training and assessment methods that can help improve workers’ competence and performance. By following this guide, you will be able to implement effective manual handling policies and procedures in your organization, and ensure the health and safety of your workers and yourself.
What is Manual Handling?
Manual handling is a term used to describe the various physical activities that involve lifting, holding, putting down, pushing, pulling, carrying or moving an object or a load by one or more workers. This can include animate objects such as people or animals, or inanimate objects like boxes, tools, or equipment.
Manual handling can be classified into four categories:
- Lifting and lowering: This involves raising or lowering an object from one level to another, such as from the floor to a shelf, or from a conveyor belt to a pallet.
- Carrying: This involves holding or supporting an object while moving from one place to another, such as from a warehouse to a truck, or from a storeroom to an office.
- Pushing and pulling: This involves applying force to move an object away from or towards the body, such as pushing a trolley, or pulling a rope.
- Manipulating: This involves changing the position or orientation of an object without moving it from one place to another, such as turning a valve, or twisting a screwdriver.
Manual handling can be performed manually by using the hands or arms only, or by using aids or equipment such as handles, straps, levers, wheels, or cranes. Manual handling can also be performed individually by one worker, or collectively by two or more workers.
Why is Manual Handling Important?
Manual handling is important because it is essential to many jobs and tasks in different industries and sectors. Manual handling can help workers perform their work efficiently and effectively, and achieve their goals and objectives. For example, manual handling can help workers:
- Transport materials or products from one place to another
- Load or unload vehicles or containers
- Assemble or disassemble parts or components
- Install or repair equipment or machinery
- Handle patients or animals
- Perform cleaning or maintenance tasks
However, manual handling can also pose significant hazards and risks to workers’ health and safety if it is not performed correctly. Improper manual handling can cause injuries to the muscles, bones, joints, ligaments, tendons, nerves, blood vessels, or organs of the body. These injuries can range from minor cuts and bruises to serious fractures and dislocations. Improper manual handling can also cause long-term health problems such as chronic pain, inflammation, degeneration, disability, or disease. These health problems can affect not only the physical well-being of workers but also their mental and emotional well-being.
Therefore, it is important to prevent and reduce the hazards and risks of manual handling by following the legal requirements and best practices for manual handling. By doing so, you will be able to protect your workers and yourself from harm, and promote a healthy and safe working environment.
What are the Hazards and Risks of Manual Handling?
The hazards and risks of manual handling depend on various factors that affect the difficulty and complexity of the task. These factors include:
- The task: The type, frequency, duration, speed, and sequence of manual handling activities can affect the level of physical effort, stress, and strain required by workers. For example, lifting heavy objects repeatedly for a long time can be more hazardous than lifting light objects occasionally for a short time.
- The individual: The physical characteristics, capabilities, and limitations of workers can affect their ability and suitability to perform manual handling tasks. For example, age, gender, height, weight, strength, flexibility, fitness, health condition, and prior injuries can influence how workers handle loads.
- The load: The weight, size, shape, and surface of the object or material being handled can affect how easy or difficult it is to grip, lift, carry, push, pull, or manipulate it. For example, a large, heavy, bulky, or slippery load can be more hazardous than a small, light, compact, or stable load.
- The environment: The physical conditions and layout of the workplace can affect the accessibility and safety of manual handling tasks. For example, poor lighting, ventilation, temperature, humidity, noise, vibration, or space can create hazards for manual handling. Additionally, uneven, slippery, or cluttered floors, or obstacles such as stairs, doors, or furniture can increase the risk of accidents or injuries.
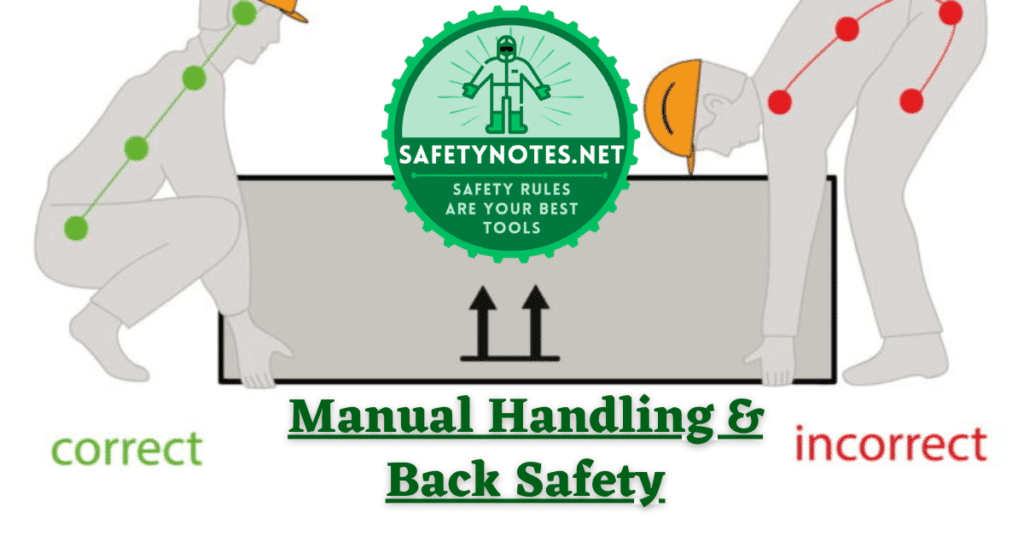
The hazards and risks of manual handling can result in various types of injuries or health problems, such as:
- Musculoskeletal disorders (MSDs): These are injuries or disorders that affect the muscles, bones, joints, ligaments, tendons, nerves, blood vessels, or organs of the body. MSDs can be caused by excessive or prolonged force, pressure, tension, compression, shear, torsion, or vibration applied to the body during manual handling. MSDs can affect any part of the body, but they are most common in the back, neck, shoulders, arms, hands, legs, and feet. MSDs can manifest as pain, stiffness, swelling, inflammation, bruising, bleeding, numbness, tingling, weakness, or loss of function. MSDs can be acute (occurring suddenly or immediately after manual handling) or chronic (developing gradually or persisting over time). Some examples of MSDs are:
- Back injuries: These are injuries that affect the spine or the surrounding muscles, ligaments, or discs. Back injuries can be caused by lifting heavy or awkward loads, bending or twisting the spine, maintaining poor posture, or experiencing sudden impact or jolt. Back injuries can result in lower back pain, sciatica, slipped disc, spinal fracture, or spinal cord damage.
- Sprains and strains: These are injuries that affect the ligaments (tissues that connect bones) or the muscles and tendons (tissues that connect muscles to bones). Sprains and strains can be caused by overstretching, tearing, or rupturing these tissues during manual handling. Sprains and strains can result in pain, swelling, bruising, inflammation, reduced range of motion, or loss of strength.
- Fractures and dislocations: These are injuries that affect the bones or the joints. Fractures and dislocations can be caused by breaking or displacing the bones during manual handling. Fractures and dislocations can result in pain, swelling, deformity, bleeding, nerve damage, or impaired mobility.
- Hernias: These are injuries that occur when an organ or tissue protrudes through a weak spot in the abdominal wall. Hernias can be caused by increased pressure in the abdomen during manual handling. Hernias can result in pain, bulging, discomfort, nausea, vomiting, or bowel obstruction.
- Repetitive strain injuries (RSIs): These are injuries or disorders that affect the nerves, muscles, tendons, or blood vessels of the body. RSIs can be caused by repeated or prolonged movements of the same body part during manual handling. RSIs can affect any part of the body but they are most common in the hands, wrists, elbows, shoulders, neck, and eyes. RSIs can manifest as pain, stiffness, swelling, inflammation, numbness, tingling
- RSIs can be acute (occurring suddenly or immediately after manual handling) or chronic (developing gradually or persisting over time). Some examples of RSIs are:
- Carpal tunnel syndrome: This is a condition that affects the median nerve that runs from the forearm to the hand through a narrow passage called the carpal tunnel. Carpal tunnel syndrome can be caused by compressing or inflaming this nerve during manual handling. Carpal tunnel syndrome can result in pain
- Loss of coordination in the hand and fingers
- Tendonitis: This is a condition that affects the tendons (tissues that connect muscles to bones). Tendonitis can be caused by overusing or injuring these tissues during manual handling. Tendonitis can result in pain
- Swelling
- Inflammation
- Reduced range of motion
- Loss of strength in the affected body part
- Bursitis: This is a condition that affects the bursae (small fluid-filled sacs that cushion the joints). Bursitis can be caused by irritating or inflaming these sacs during manual handling. Bursitis can result in pain.
- The severity and frequency of these injuries or health problems can vary depending on the individual and the situation. Some workers may experience mild or occasional symptoms that do not interfere with their work or daily activities. Others may suffer from severe or chronic conditions that require medical attention or affect their quality of life. In some cases, these injuries or health problems can be fatal or cause permanent disability.
- Therefore, it is important to identify and assess the hazards and risks of manual handling in your workplace and take appropriate measures to eliminate or minimize them. By doing so, you will be able to prevent and reduce the occurrence and impact of these injuries or health problems on your workers and yourself.
Best practices for manual handling : Safe Manual Handling
Manual handling is a common activity in many workplaces, but it can also pose significant risks to workers’ health and safety. To prevent and reduce the hazards and risks of manual handling, you should follow the legal requirements and best practices for manual handling. Here are some of the best practices for manual handling that can help you perform your work safely and efficiently:
- Conduct a manual handling risk assessment: Before you start any manual handling task, you should identify and evaluate the potential hazards and risks involved. You can use the TILE method to assess the task, individual, load, and environment factors that affect the difficulty and complexity of the task. You should also consult with your workers and supervisors to get their input and feedback on the manual handling risks and solutions.
- The TILE method is a technique for conducting a manual handling risk assessment. It stands for Task, Individual, Load, and Environment. It helps you to identify and evaluate the potential hazards and risks involved in lifting, holding, putting down, pushing, pulling, carrying or moving an object or a load by one or more workers. By using the TILE method, you can improve the health and safety of yourself and others who perform manual handling tasks.
- Here is a brief explanation of what each letter of the TILE method means:
- T – Task: This means considering the manual handling activity itself, such as the type, frequency, duration, speed, and sequence of movements. You should also look at how the task may affect your health and safety, such as whether it involves repetitive or strenuous movements, long distances, or uneven weight distribution.
- I – Individual: This means considering the person who will be carrying out the manual handling activity, such as yourself or another colleague. You should also look at how your physical characteristics, capabilities, and limitations may affect your ability and suitability to perform the task. For example, you should consider your age, gender, height, weight, strength, flexibility, fitness, health condition, and prior injuries.
- L – Load: This means considering the object or material that is being moved, and looking at how it may affect your health and safety. For example, you should consider the weight, size, shape, and surface of the load. You should also look at whether the load is particularly heavy, bulky, hard to grasp or unstable.
- E – Environment: This means considering the area in which the load is being moved, and looking at how it could make the manual handling task unsafe. For example, you should consider the physical conditions and layout of the workplace. You should also look at whether there are any hazards such as poor lighting, ventilation, temperature, humidity, noise, vibration, or space. Additionally, you should look at whether there are any obstacles such as uneven, slippery, or cluttered floors, or barriers such as stairs, doors, or furniture.
- By following the TILE method, you can plan and prepare your manual handling task carefully, and take appropriate measures to eliminate or minimize the hazards and risks. You can also use mechanical tools and aids, wear suitable clothing and footwear, know your limits, and use proper techniques to handle loads safely and efficiently .
- Provide your employees with the right manual handling training: You should ensure that your workers have the necessary knowledge and skills to perform manual handling tasks safely and correctly. You should provide them with appropriate training on the principles, techniques, and procedures of manual handling, as well as the use of any aids or equipment that can assist them. You should also monitor and evaluate their performance and provide them with regular feedback and refresher training.
- Use mechanical tools and aids: Whenever possible, you should use mechanical tools and aids to reduce or eliminate the need for manual handling. For example, you can use trolleys, carts, hoists, cranes, conveyors, or forklifts to transport or lift heavy or bulky loads. You should also ensure that these tools and aids are suitable, available, accessible, maintained, and operated correctly.
- Plan before you start: You should plan your manual handling task carefully and prepare everything you need before you start. For example, you should check the load for any hazards such as sharp edges, loose parts, or spillages. You should also clear the path for any obstacles or hazards such as stairs, doors, or furniture. You should also decide where and how you will place the load at the destination.
- Wear the right clothing: You should wear clothing that is comfortable, flexible, and suitable for the task and the environment. You should avoid wearing clothing that is too loose, too tight, or has dangling parts that can get caught or snagged on the load or the surroundings. You should also wear appropriate footwear that is comfortable, supportive, and slip-resistant.
- Know your limits: You should know your own physical capabilities and limitations and do not attempt to handle loads that are beyond your capacity. You should also avoid lifting loads that are too heavy, too large, too high, or too low for you. You should also ask for help from your colleagues or supervisors if you need assistance with manual handling tasks.
- Push rather than pull: When you have to move a load horizontally by pushing or pulling it, you should prefer pushing rather than pulling it. Pushing allows you to use your body weight and leg muscles to move the load more easily and safely. Pulling can cause more strain on your back, neck, shoulders, arms, and hands. However, you should also avoid pushing loads that are too heavy or unstable for you.
- Bend your knees: When you have to lift or lower a load vertically by using your hands or arms, you should bend your knees rather than your back. Bending your knees allows you to use your leg muscles to lift or lower the load more easily and safely. Bending your back can cause more strain on your spine, muscles, ligaments, or discs. However, you should also avoid lifting or lowering loads that are too heavy or awkward for you.
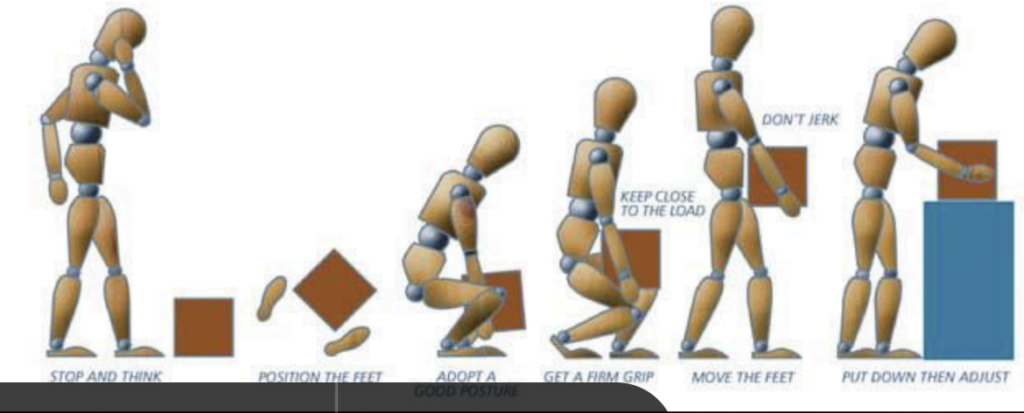
By following these best practices for manual handling, you will be able to perform your work safely and efficiently, and protect yourself and others from harm.
Safety regulations from regulatory websites on Manual handling
To prevent and reduce the hazards and risks of manual handling, you should follow the safety regulations from regulatory websites on manual handling. Here are some of the safety regulations from different sources that can help you perform your work safely and efficiently:
- The Manual Handling Operations Regulations 1992 (MHOR) are guidance designed for employers, managers and safety representatives in the UK. They explain how to avoid, assess and reduce the risk of injury from manual handling. The guidance was amended by the Health and Safety Regulations in 2002.
- The Occupational Safety and Health Administration (OSHA) is a federal agency that regulates workplace safety and health in the US. OSHA has standards and guidelines for manual handling, such as the Ergonomics Program Standard, the General Duty Clause, and the Technical Manual Chapter on Back Disorders and Injuries.
- The International Labour Organization (ILO) is a specialized agency of the United Nations that sets international standards and policies for decent work. ILO has conventions and recommendations on manual handling, such as the Occupational Safety and Health Convention, the Occupational Health Services Convention, and the Code of Practice on Safety and Health in Agriculture .
In conclusion, manual handling is a common activity in many workplaces, but it can also pose significant risks to workers’ health and safety. To prevent and reduce the hazards and risks of manual handling, you should follow the legal requirements and best practices for manual handling. You should also consult the safety regulations from regulatory websites on manual handling, such as the MHOR, OSHA, EU-OSHA, and ILO. By doing so, you will be able to protect yourself and others from harm, and perform your work safely and efficiently.