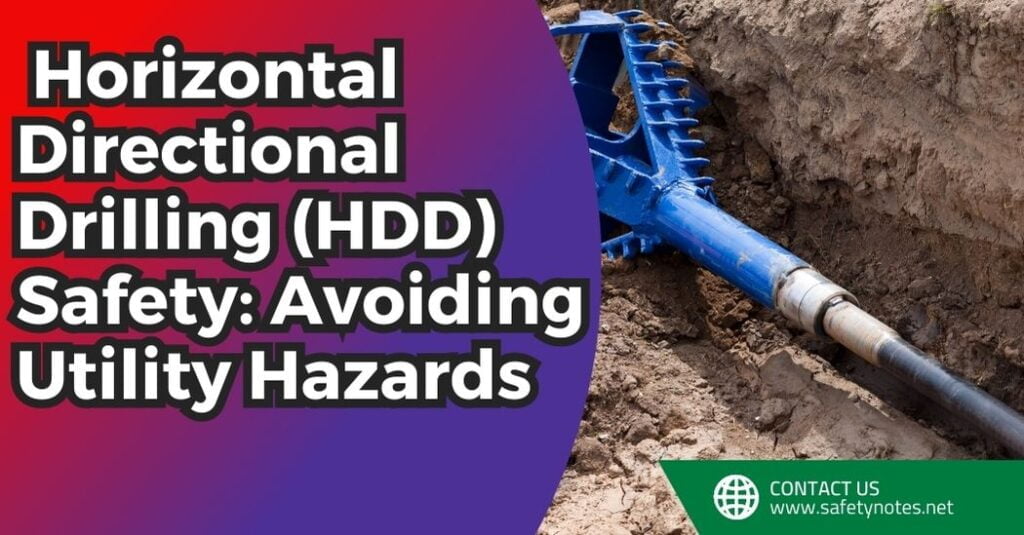
Introduction
Horizontal Directional Drilling (HDD) is a trenchless method of installing underground utilities. While offering many benefits, including minimal surface disruption and the ability to navigate around obstacles, HDD poses significant risks if operators inadvertently strike existing underground utilities. The aftermath of such an incident could be catastrophic, from fires and explosions to electrocutions. Ensuring safe and efficient HDD operations is therefore paramount.
Horizontal Directional Drilling – HDD: A Brief Overview
Horizontal Directional Drilling (HDD) is a groundbreaking technique used primarily for installing pipes, conduits, and cables underground. Most prevalently employed in urban settings or areas where conventional digging methods are risky, HDD comes with its own set of challenges, mainly due to the decreased visibility during operations.
How HDD Equipment Functions
To fully grasp the risks involved, it’s essential to understand the HDD process:
- Drill the Pilot Bore: Operators create a pilot bore, extending from the entry to the exit point. Throughout this, a “tracker” ensures the drill stays on the predefined path, avoiding utility lines.
- Enlarge the Bore: After completing the pilot bore, operators use a back reamer to widen the bore.
- Install Conduit/Casing: Once the bore is sufficiently large, the conduit or casing is pulled into place.
Images depicting these steps can be sourced from the International Society for Trenchless Technology.
Understanding the Risks: The Kansas City Incident
In 2013, a tragic mishap occurred during an HDD operation in Kansas City, MO. Workers mistakenly identified electrical lines as gas lines. The subsequent drilling damaged a gas line, leading to an explosion and fire. This incident underscores the paramount importance of accurately identifying underground utilities.
Preventing Utility Line Strikes: Best Practices
Avoiding underground utilities is the cornerstone of safe HDD operations. Here’s a comprehensive guide on how to ensure safety:
- Visual Inspections: Before drilling, inspect the entire planned digging path, looking for indicators of utilities such as gas meters and manhole covers.
- Collaborate with Utility Companies: Direct contact with utility firms can provide up-to-date and accurate information about underground utilities.
- Potholing: This method involves digging vertical holes to expose and verify the location of utilities. It’s a practical approach that provides a clear visual of where utilities are located.
- Call Before You Dig: This service, accessed by dialing 811, provides insights into where utilities are buried.
- Regular Training: Equip your HDD operators and trackers with comprehensive training, ensuring they’re prepared to respond to emergencies and unexpected situations.
Safety Measures for HDD Operations
Safety should always be the top priority. Following these precautions can significantly mitigate risks:
- Conduct Site-Specific Safety Assessments: Tailor your safety protocols according to the specifics of each drilling site.
- Walkthroughs: Ensure that the HDD machine operator and tracker are familiar with the planned drill path and potential hazards.
- Effective Communication: Equip your team with hand signals and radios to facilitate seamless communication.
- Monitor Drilling Progress: Use trackers to constantly monitor the drilling, allowing for immediate action if any issues arise.
Handling Gas Line Strikes
If a gas line is struck during Horizontal Directional Drilling operations, the resultant leak poses significant explosion and fire risks. Gas is highly flammable and can ignite due to various factors. Recognizing a leak early is crucial. Signs include:
- Dirt or debris being forcefully ejected from the ground.
- Unusual noises near a gas line, such as hissing or whistling.
- A distinctive sulfur-like odor, although it’s essential to note that not all gas is odorized.
Emergency Protocols
Having a well-defined Emergency Action Plan (EAP) is essential. In case of a suspected gas leak:
- Evacuate Immediately: Prioritize getting all workers to safety.
- Notify Authorities: Once in a safe location, call 911 and the utility company.
- Prohibit Open Flames: Ensure there are no open flames or smoking near the work area.
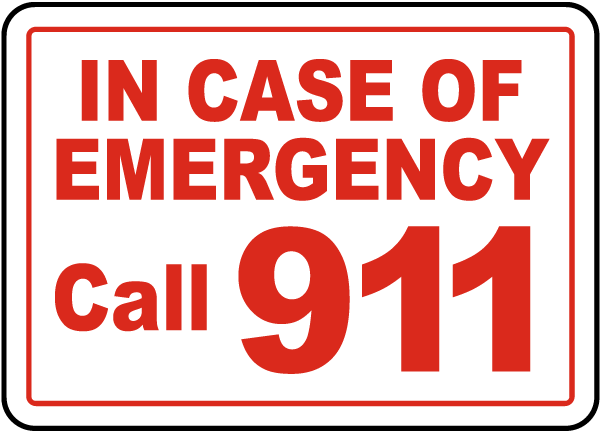
Training and Awareness
Training is the foundation of safe HDD operations. All workers should be aware of how to:
- Identify utility lines.
- Clarify any ambiguities from surface markings.
Avoiding Mistakes during Drilling Operations
When planning and conducting HDD operations, multiple factors can contribute to mistakes, which may result in devastating consequences. Hence, it’s essential to keep a proactive approach, fostering constant vigilance and comprehensive training.
Quality Checks and Safety Monitoring
1. Continuous Monitoring of Drill Path
Throughout the drilling process, constant checks and evaluations are essential. While trackers play a pivotal role in ensuring the drill remains on the predetermined path, additional supervision can further minimize risks. Using advanced tracking devices and software can offer real-time feedback, helping in immediate course correction if any deviation occurs.
2. Regular Equipment Inspection
Equipment failure can be catastrophic during drilling. Regular inspections, maintenance, and timely replacements can prevent accidents. This is not just limited to the primary HDD machine but extends to all auxiliary tools and equipment used.
Training: The Heart of Safety Protocols
Every piece of equipment and every safety protocol is only as effective as the individual operating or adhering to it. Training is paramount.
1. Regular Skill Upgradation
The construction and drilling industry is evolving rapidly, with new technologies and techniques emerging. Regular workshops and skill upgradation sessions ensure workers are always at the top of their game, familiar with the best and latest in the industry.
2. Mock Drills and Simulations
Simulated scenarios of potential accidents and how to handle them can help workers respond better in real emergencies. Such drills make them familiar with the steps they need to follow, ensuring a more organized and efficient response to crises.
3. On-Site Safety Officers
Having dedicated safety officers on site who can monitor operations, offer guidance, and ensure safety protocols are being followed can be a game-changer. These officers can also conduct surprise drills, keep the crew on their toes, and ensure adherence to safety protocols is not just a mandate but a habit.
The Role of Technology in Ensuring Safety
While manual checks and training are crucial, leveraging technology can elevate safety measures.
1. Advanced Tracking Systems
Systems that employ AI and machine learning can predict potential obstacles and offer course corrections, sometimes even before human trackers can identify the problem.
2. Real-Time Communication Tools
Instant communication tools that allow seamless communication between the tracker, operator, and the supervisory team can facilitate immediate action, ensuring that any deviations or potential hazards are addressed instantly.
3. Safety Wearables
Modern safety wearables are equipped with sensors that can monitor vital signs of workers, detect gas leaks, and even send immediate alerts in case of sudden falls or injuries. These can be indispensable in ensuring the safety of every individual on the site.
Conclusion
Safety during HDD operations isn’t just about following a checklist; it’s about creating an ecosystem where safety is inherent to every process, every action. Through continuous monitoring, regular training, and the effective use of technology, it’s possible to mitigate risks, ensuring not only the successful completion of projects but also the well-being of every worker involved.
FAQs: Horizontal Directional Drilling (HDD) Operations
1. What is Horizontal Directional Drilling (HDD)?
Horizontal Directional Drilling (HDD) is a trenchless construction method used to install underground utilities such as pipes, conduits, and cables without disturbing the ground surface. It’s an eco-friendly and less disruptive method than traditional excavation.
2. How does HDD differ from traditional drilling methods?
Unlike traditional drilling that requires digging trenches, HDD creates a bore path underground using a surface-launched drilling rig. This results in minimal environmental impact, reduced traffic disruption, and faster installation times.
3. What are the main components of an HDD system?
An HDD system comprises a drilling rig, a fluid mixing system, a fluid recycling system, tracking equipment, and a reamer. The drilling rig pushes and rotates the drill string, while the fluid system lubricates, cools, and removes drilled cuttings.
4. How do you ensure safety during HDD operations?
Safety in HDD operations involves continuous monitoring of the drill path, regular equipment inspection, and rigorous training of personnel. Advanced tracking devices, on-site safety officers, and safety wearables further enhance safety measures.
5. Why is training important for HDD operations?
Training ensures that operators and other personnel are aware of the latest safety protocols and techniques. It equips them to handle emergencies efficiently, reduces the risk of accidents, and ensures successful and safe project completion.